About cement
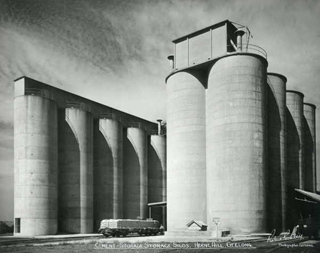
Production trends and usages
World Production and World trends
Globally, more than 1,000 cement producers operate over 2,300 integrated cement plants and over 600 grinding stations. Five countries account for nearly three-quarters of the world's cement production: China leads with a 53 % share, followed by India (320 MT) with a 7% , Vietnam (96,5 MT) with a 2%, the United States (88,9 MT) with a 2%, and Indonesia (64,2 MT) with a 1% share.
The speed of the COVID-19 recovery is expected to vary significantly across countries, depending on multiple factors such as the severity and timing of the pandemic itself, lockdown measures, access to medical interventions and vaccines, export market exposure, and labour market dynamics and demographics.
Once countries begin to reopen post-pandemic, consumption of cement and concrete is expected to gradually recover, fueled by economic growth, urbanization, and population growth, especially in emerging markets. The industry's biggest challenges—and opportunities - are longer-term: To survive and flourish, companies must prioritize sustainability and raise their environmental standards. Governments, investors, and the general public increasingly are pushing companies to reduce their carbon footprint. Cement companies that prioritize sustainability even during this difficult period are likely to emerge as the winners in the next cycle. Many companies are already taking significant measures towards decarbonization.
Main world producers
Cement production (Million tonnes) |
||||||||
Country |
2001 |
2005 |
2010 |
2015 |
2016 |
2017 |
2018 |
2019 |
China |
661,0 |
1079,6 |
1881,9 |
2350,0 |
2403,0 |
2316,3 |
2176,7 |
2300,0 |
India |
102,9 |
146,8 |
220,0 |
270,0 |
289,3 |
285,0 |
327,7 |
320,0 |
EU28* |
225,8 |
251,1 |
192,1 |
167,2 |
169,1 |
175,1 |
179,8 |
182,1 |
USA |
88,9 |
99,4 |
65,2 |
83,4 |
84,7 |
86,1 |
87,8 |
88,6 |
Brazil |
39,4 |
39,2 |
59,1 |
72,0 |
57,6 |
54,0 |
53,5 |
53,4 |
Turkey |
30,0 |
45,6 |
62,7 |
71,4 |
75,4 |
80,6 |
72,5 |
57,0 |
Russian Federation |
28,7 |
49,5 |
50,4 |
69,0 |
55,0 |
54,7 |
53,7 |
54,1 |
Indonesia |
31,1 |
36,1 |
39,5 |
65,0 |
61,3 |
68,0 |
70,8 |
64,2 |
South Korea |
52,0 |
49,1 |
47,4 |
63,0 |
56,7 |
57,9 |
55,0 |
56,4 |
Japan |
79,5 |
72,7 |
56,6 |
55,0 |
53,4 |
55,5 |
55,3 |
55,2 |
Saudi Arabia |
20,0 |
26,1 |
42,5 |
55,0 |
55,9 |
47,1 |
42,2 |
42,2
|
Mexico |
33,2 |
38,1 |
34,5 |
39,8 |
42,4 |
42,8 |
42,8 |
47,5 |
Germany |
32,1 |
31,9 |
29,9 |
31,1 |
32,7 |
34,0 |
33,7 |
34,2 |
Italy |
39,8 |
46,4 |
34,4 |
20,8 |
19,3 |
19,3 |
19,3 |
19,2 |
France |
19,1 |
21,7 |
18,0 |
15,6 |
15,9 |
16,9 |
16,5 |
16,5 |
South Africa |
8,4 |
12,1 |
10,9 |
14,0 |
13,6 |
13,2 |
12,5 |
12,4 |
Canada |
12,1 |
13,5 |
12,4 |
12,5 |
11,9 |
12,7 |
13,3 |
13,4 |
Argentina |
5,5 |
7,6 |
10,4 |
12,2 |
10,9 |
12,0 |
11,8 |
11,5 |
United Kingdom |
11,9 |
11,6 |
7,9 |
9,6 |
9,4 |
9,4 |
9,2 |
9,1 |
Australia |
6,8 |
9,1 |
8,3 |
9,3 |
10,0 |
10,0 |
9,8 |
10,0 |
*EU28 data is compiled using latest available data – EU27 will be introduced as of 2020
Source: https://cembureau.eu/media/1sjf4sk4/cembureau-activity-report-2020.pdf
European Production
Looking at the CEMBUREAU and EU28 cement production and consumption data from 2019, we can see that the CEMBUREAU production and clinker exports, dropped by 10.4 Mt to 261.9 Mt, close to the 2014 and 2015 production levels, whereas the EU-28 production was almost constant at 190.4 Mt. This is mainly due to decreasing production in Turkey, partially compensated by increasing clinker exports.
The cement consumption dropped for CEMBUREAU members, from 237 Mt in 2018 to 219 Mt in 2019. The EU28 countries saw an increase of 2 Mt to 169 Mt. Individual CEMBUREAU members experienced wide differences in consumption from 2018 to 2019.
Serbian Production
After 2013 and 2014 when production of cement in Serbian cement plants was almost constant, trend is changing and starting by 2015 production and consumption of cement are rising. The trend of cement production increase continued throughout the pandemic (2020) and reached up to 9.8% compared to 2019, when production of 2.15 million tons of cement was recorded. Consumption of cement in 2020 reached 2.70 million tons, which represents an increase of 14.7% compared to 2019. year.
Source: Statistical Office of the Republic of Serbia
Market demands
Increased use of cement allowed for an accelerated growth of the construction industry, particularly of concrete constructions, but also the reverse, the development of the construction industry presented cement producers with increased requirements, which were gradually overcome.
Designers and drafters require high-strength cements, with particular emphasis on the dynamics of hardening, but other specific characteristics as well: decreased heat of hydration for the construction of massive concrete constructions, increased chemical resistance (primarily sulfates and acid medias) , less shrinking and other demands. In all this, maximum attention is dedicated to uniformity of content, meaning at the same time the usable qualities of cement.
Cement is an unavoidable raw material in all aspects of construction, from construction of house buildings, business and industrial buildings and installations, bridges, tunnels and roads, ending with subterranean works and subsoils. In other words, whenever and wherever concrete and mortar are required, that is:
- Superplasticized concrete with high compressive strength – HPC concretes (High Performance Concretes);
- Prestressed constructions and concrete products;
- Precast concrete (lamp-post, kerb blocks, bearers for roof constructions, bearers for halls and crane rail);
- Concrete slabs for courtyards and squares;
- Concrete products requiring rapid de-installation or rapid de-installing of forms;
- Lightweight concretes, that is “cellular” or “hollow” concretes, gas concrete and foamed concrete;
- Classic concrete (pumping, self-compacting);
- Cement and flexible mortar;
- Dry mortars (adhesives for ceramic tiles and polystyrene, dry mixtures for concrete floors and pointing, ready-mix mortars for sanation or intended for injecting, grouting, mortars and mortars for plastering).
Up to now, concrete as a construction material has developed towards improvement of compressive strengths while in the future it is to be expected that improvements in other features will be attained as well, such as modulus of elasticity, flexural strength, dynamic strength, permeability and durability. Certain improvements have been attained in some mineral additives contained in cement, such as granulated blastfurnace slag, fly ash, limestone, etc.