About cement
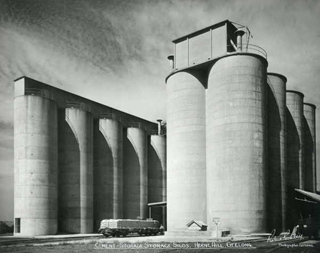
Production
Steps and phases
Production of Portland cement is a complex technological process that consists of two basic steps. In the first, through heat processing entering raw materials are fundamentally altered creating cement clinker. In the second, by grinding and milling clinker wit gypsum the final product – cement – is manufactured.
The general technological scheme of production of Portland cement , which includes processes with raw materials and the final product consist of the following eight phases :
- Extraction of raw materials used in cement production;
- Preparation of raw materials (including grinding and mixing);
- Warehousing of meal;
- Baking of raw material meal (production of clinker);
- Maturing of clinker;
- Milling of clinker into cement;
- Warehousing of cement
- Packing and dispatch.
Raw materials
The basic raw materials used to prepare the mixture which through baking converts into clinker are:
- Raw materials of carbonate character (limestone and some kinds of marl with a high content of CaCO3);
- Raw materials of an acid character (clays, shales, marl clay , tuff, pozzolana and others).
Corrective raw materials, whose basic role is to improve the chemical composition of the mixture are:
- Raw materials of a silicate character (quartz sand, tuff and other mineral materials of natural or synthetic origin);
- Raw materials with a high content of iron oxides (pyrit burns) and similar.
Raw materials that are in the process of obtaining the final product mixed with clinker are gypsum and additives such as natural and synthetic pozzolana, blast furnace slag, limestone and others.
Alternative raw materials
The use of alternative raw materials such as blast furnace slag, fly ash from thermal power plants, silica fume and others in the process of production of clinker for cement have a significant positive impact on environmental protection.
The gathering of these materials on the soil create air pollution while gathering in lakes and other fluid flows releases toxic materials that are normally present in small quantities. A particularly convenient circumstance is the fact that heavy metals contained in cement practically are not released from finalized cement products – concrete and plaster.
The use of alternative raw materials in clinker production or as a substitute for a portion of clinker in cement reduces consumption of natural non-renewable energy sources and emissions of CO2 (caused by the reaction of de-carbonation from raw materials and burning of fuel). Each procedure of reduction of the amount of clinker in cement leads to savings of raw materials, fuel and causes reductions of CO2 emissions into the atmosphere in the equal percentage.
Production of clinker
The process of cement clinker production is performed in a broad temperature band and includes a number of processes and reactions of decomposition and synthesis.
In a temperature band of 50-900 oC water is extracted. Warming of the meal from 50-100 oC causes mechanically linked water to evaporate, while chemically linked water evaporates in the band from 100-300 oC. At temperatures above 200 oC processes of dehydration are carried out (a chemical reaction that results in the loss of water from molecules) as well as dehydroxylation (a chemical reaction that results from the separation of hydroxyl, –OH group from organic compounds) of clay substances. The temperature processes of dehydration and dehydroxylation depend on the kind of clay minerals contained in the meal.
At temperatures of 900-1100 oC a process of thermal dissociation of carbonates is carried out, with the decomposition of limestone (CaCO3), dolomite (CaCO3 x MgCO3) or magnesite (MgCO3).
In the temperature band of 1000-1200 oC the first reactions between the CaO in limestone and acid oxides in clay (SiO2, Al2O3 and Fe2O3) begin, meaning that the reaction of creation of clinker mineral and the creation of the final product – cement clinker. This reaction of creation or synthesis of clinker mineral, due to the presence of mineralizers and flux starts already above 700 oC. Thereby it has been proven that:
- Even below 800 oC it is possible to create CaO x Al2O3 and also CaO x Fe2O3 or CF;
- Between 800-900 oC begins the process of creation of CaO x SiO2 or CS, which transforms at around 1000 oC into compounds with a higher content of CaO;
- Between 900-950 oC merges 5CaO x 3Al2O3 or C5A3 that is C12A7 which as such may be found in the final product;
- Between 950-1200 oC starts the creation of 2CaO x SiO2 or C2S , which is also to be found in the final product;
- Between 1200-1300 oC starts the creation of 3CaO x Al2O3 or C3A, which probably passes into aluminoferrite phase 4CaO x Al2Os x Fe2O3 or C4AF;
- Between 1200-1450 oC the sintering phase comes the creation of 3CaO x SiO2 or C3S as the main and basic clinker mineral.
In the sintering zone, that is at temperatures of 1450 oC or higher, a state of balance is established. The permanent maintaining of this stage is achieved by sudden and as rapid as possible cooling, particularly in the interval between 1450 and 1250 oC. After cooling, which conserves its mineral content, clinker is storage in particular warehouses. It stays there for a period of time before milling in order to free lime (CaOfree) which may have remained through reaction with moisture and CO2 from air.
Production of cement
The final product – Portland cement – is obtained by milling clinker with 2-4% gypsum in steel bearing mills. Gypsum is added in order to regulate the setting time of the cement obtained.
In the milling process apart from gypsum other additives may be added to clinker, such as granulated blast furnace slag, natural and industrial pozzolana, limestone and other materials, that is done in the production of cement with additives.
You can learn more about the history of Portland cement here.
Sources:
- Petar Krolo, “Technology of Binders and Composite Materials”, Faculty of chemistry and technology, Split, 1999;
- Predrag Brzakovic, “Manual for production and application of non-metallic construction products”, Book 1, Belgrade, 2000;
- Peter C. Hewlett, ‘Lea’s Chemistry of Cement and Concrete”, fourth edition, Read Educational and Professional Publishing Ltd, London, 1998.